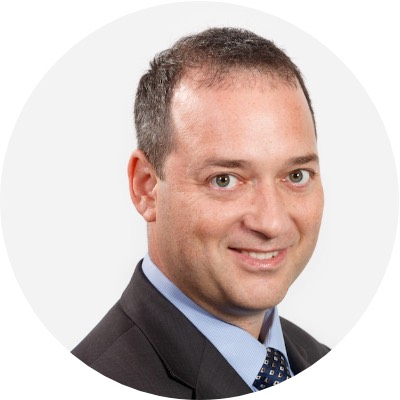
Robert Kovacs
CEO
Welcome!
Those of you who have been in any leadership role at any manufacturing company knows that the continuous improvement and productivity increase are common expectations. However, the resources in most of the cases are limited. In such a combination of limited resources and high expectations leaders should use the most effective techniques and tools to be successful. As I worked at many multinational companies in managing roles both domestically and abroad I faced these expectations. Lean as managing philosophy and approach including many practical tools can be used effectively in such an environment. Resources should focus on value added activities. Any activities that do not bring value to customer should be eliminated or reduced. Employees do not need work to harder or longer. Spending the same level of energy on the right things will automatically increase productivity. As a matter of fact employees work more efficiently and smartly then before. On the manager level also does not require costly investments or innovations to spread a lean approach along the company. Changing the mindset of employees and focusing on a lean approach is the key to success. Here we go. It is easy to say, and challenging to do. In theory, many consultant companies and trainers give lectures but only a few have personal practical experience and can say that implemented lean into the company culture and changed the mindset of people. I did this. Beyond all the theory I had the opportunity to practically implement lean into organizations with great success. I am aware of all the difficulties and barriers in real life. I encourage all leaders to take the journey as it pays back all the efforts when you see your organization grow to a level that seemed unbelievable beforehand.
Service
I offer theoretical trainings with practical tools and practical workshops taking place in GEMBA. Both in English and Hungarian languages. I do trainings for all different level in the organization from operators to top management.

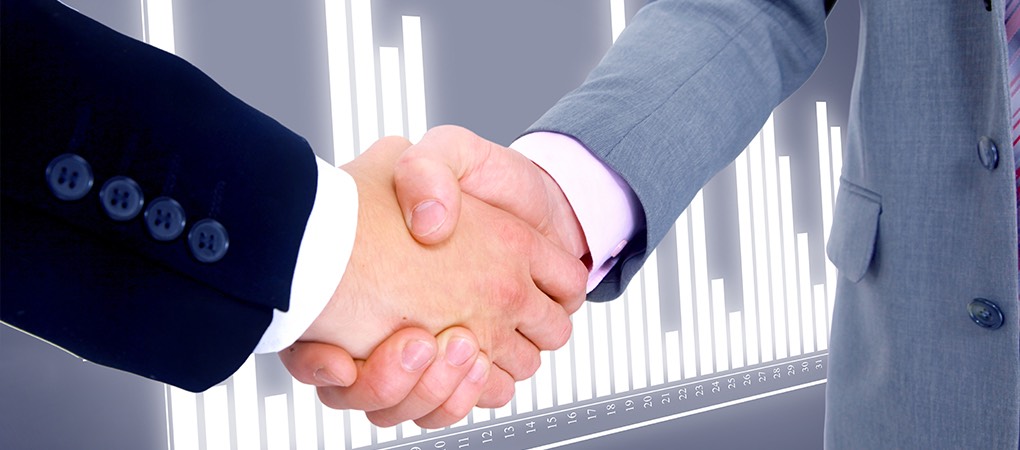
Partnership
Every organization is different. There are some common points in manufacturing mass production and certain general rules however the culture of a company and the skill and commitment level of employees are different by companies. Due to this fact, I am not offering a standard cliche that could be used by anyone, where employees get nice certificates at the end of the course but the managers will not ever see any value of the training in the key performance indicators of the company.
In alignment with the lean approach the first and most important step that I start with is to understand the needs of the customer. Define goals and be fully aware of customer needs. The following action is to measure the present level of the organization. Then I can offer what steps we should take in which sequence to reach the goals in a certain timeframe. Lean implementation should be planned by considering the company culture and understanding the unique needs of customer.
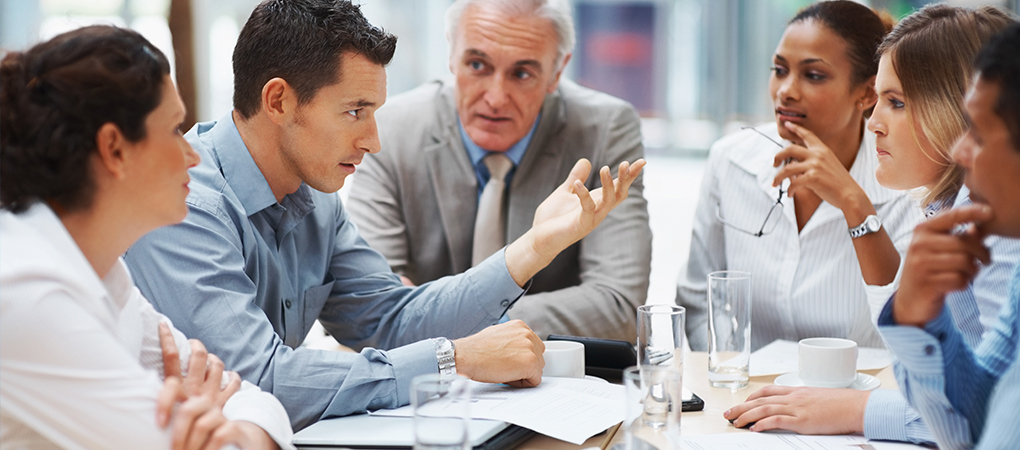
Training
Change on company level does not take place from one day to another. After setting the company strategy, goals and plans the first step is to make all employees understand where the company is going and how. Make sure all individuals are aware of the company targets and know his/her personal role on the journey. Expecting change of individuals without clarifying company goals and train them on how to change approaches and tools is the first pitfall of change management.
The first step is training and education before having any expectations. Employees must understand the lean approach. From top management down to operator level all employees should understand the lean approach and usage of lean tools in practice. Workers know the processes best therefore they are able to improve their processes most efficiently. However, for this activity, they need to have the right mentality, proper tools and support from management. I provide a wide range of training covering all areas that lean culture requires. Some of the main trainings and their thematic can be seen in trainings menu.
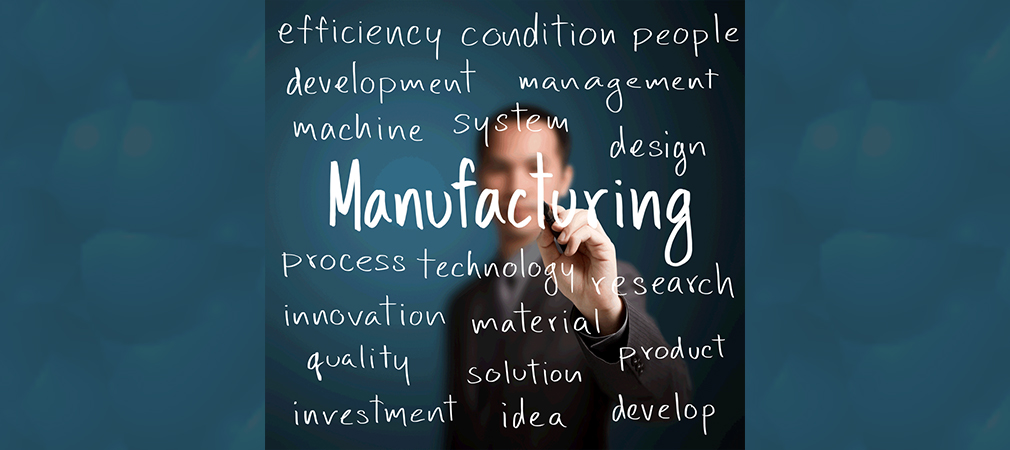
Implementation in daily life
Despite during the training most people easily understand lean principles only a few can implement them in everyday practice. I am committed making organizations implement theoretical knowledge into practice. Involving employees is one of the key factors. After the training courses employees should be able to implement the knowledge in practice. With a lean approach employees can focus their effort on the value-added processes and reduce or eliminate all the unnecessary process steps. This improvement makes their work easier and makes the company more productive. Besides I teach lean tools and approaches during the course the real value when audience goes through their processes where I can guide them on how to implement the theory into practice right at the GEMBA (The place where the value added activities happen). Due to this practical knowledge and understanding how the theory can be translated into practice company can gain benefits from the training.