Professional background
My name is Robert Kovacs. I have 25 years of experience in manufacturing mass production. I went through the career leader from process engineer up to plant manager and managing director. I worked for many highly reputed multinational companies such as GENERAL ELECTRIC, SONY, FOXCONN, PULSE, SEALED AIR, PRETTL, IDEMIA. I gained valuable personal experiences in different industries such as electronics, food, printing and laminating, automotive and bank industries. I had the opportunity to learn the lean approach and practical implementation of lean tools while I was working close to a highly respected Japanese manager – Yosihiro Sato San at SONY corporation. Under my management, SONY Hungary changed the conveyor line production to a more productive cell production system. I was the assembly plant manager of the Hungarian operation and the Six Sigma coordinator of the East European SONY factories. I learned the lean approach in Japan and had opportunities during my career to practically implement lean in many organizations. This meant significant productivity increases at many companies under my management. Due to General Electric’s 3-year Operation Leadership Program. I am a highly trained manager with full view of the supply chain. I relocated a few plants to other locations in different countries such as Germany, the USA, Finland and China. In the past 21 years, I worked in different top manager positions. Since 2014 I have been providing lean training and consultancy. In this short period I further expanded my experience in different businesses while I worked as a trainer, consultant or interim.
Specialties
- Toyota Production System
- Visual Management
- Kaizen Workshop
- Kanban System
- Change management
- Just In Time
- Time management
- Heijunka
- Poka Yoke
- Jidoka
- Shopfloor management
- Projekt management
- 5S
- Six Sigma
Markable results
Result: 110% productivity increase
Award: Sony corporate award
Project: Sealed Air: Production productivity increase
Result: 50% productivity increase
Award: Sealed Air corporate award: Gold key (2010,2012) silver key (2011)
Education
GE-OMLP: 3-year leadership program of General Electric / graduated in 2001
Awards
Sony corporate award 2003
Sealed Air Gold key (2010,2012) and Silver key (2011)
Six Sigma certificates
Trainings
- Project management
- Time management
- Presentation skills
- Manufacturing Leadership (Antwerp)
- Cell production system (Malaysia)
- Lean training series (Japan)
- Management and teambuilding (UK)
- Lean / Kaizen training (China)
Publication
“From the careless biorobots to the highly motivated well performing employees.” (Nemtörődöm biorobotoktól a lelkes és motivált munkaerőkig.”)
Certificates
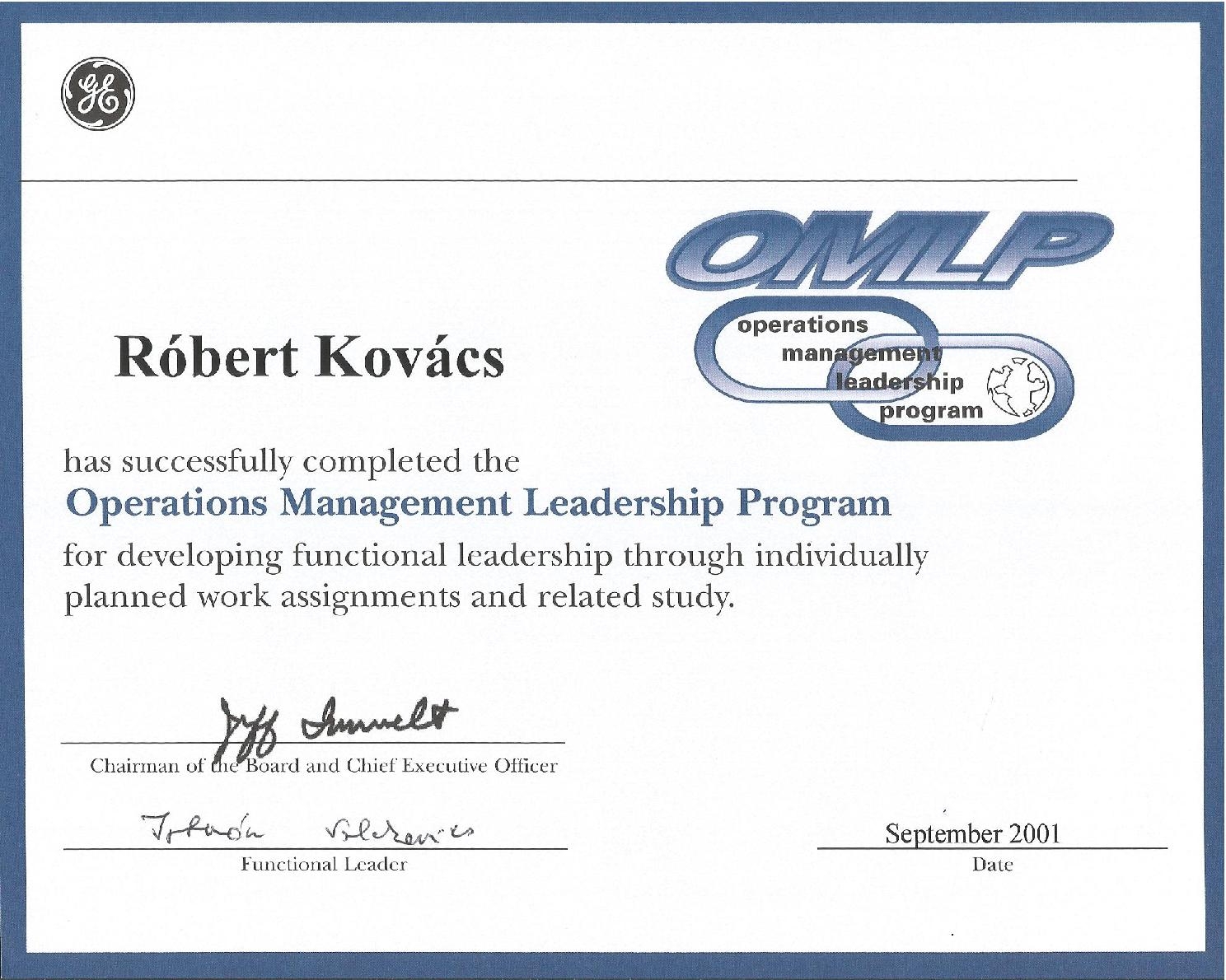
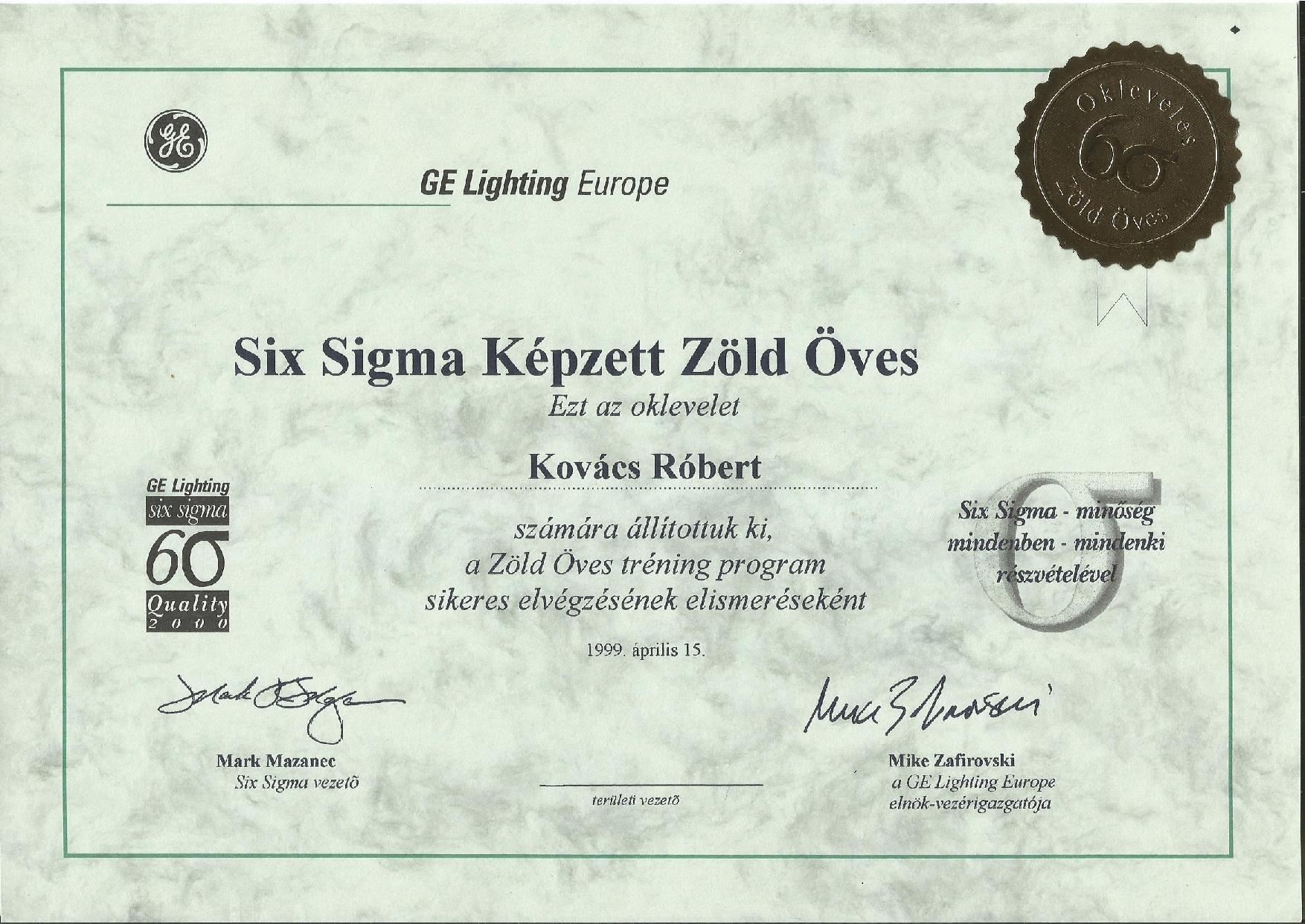
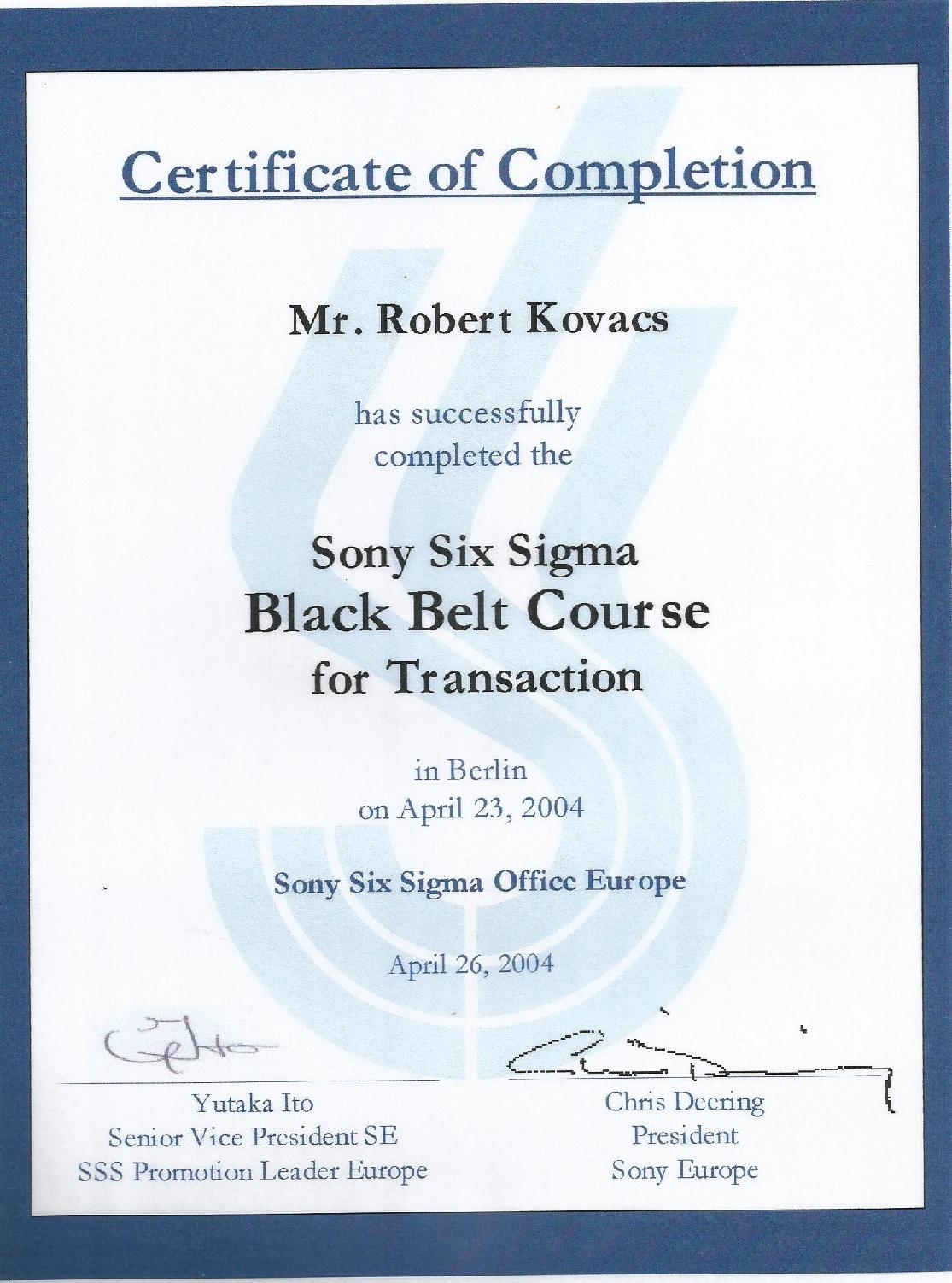
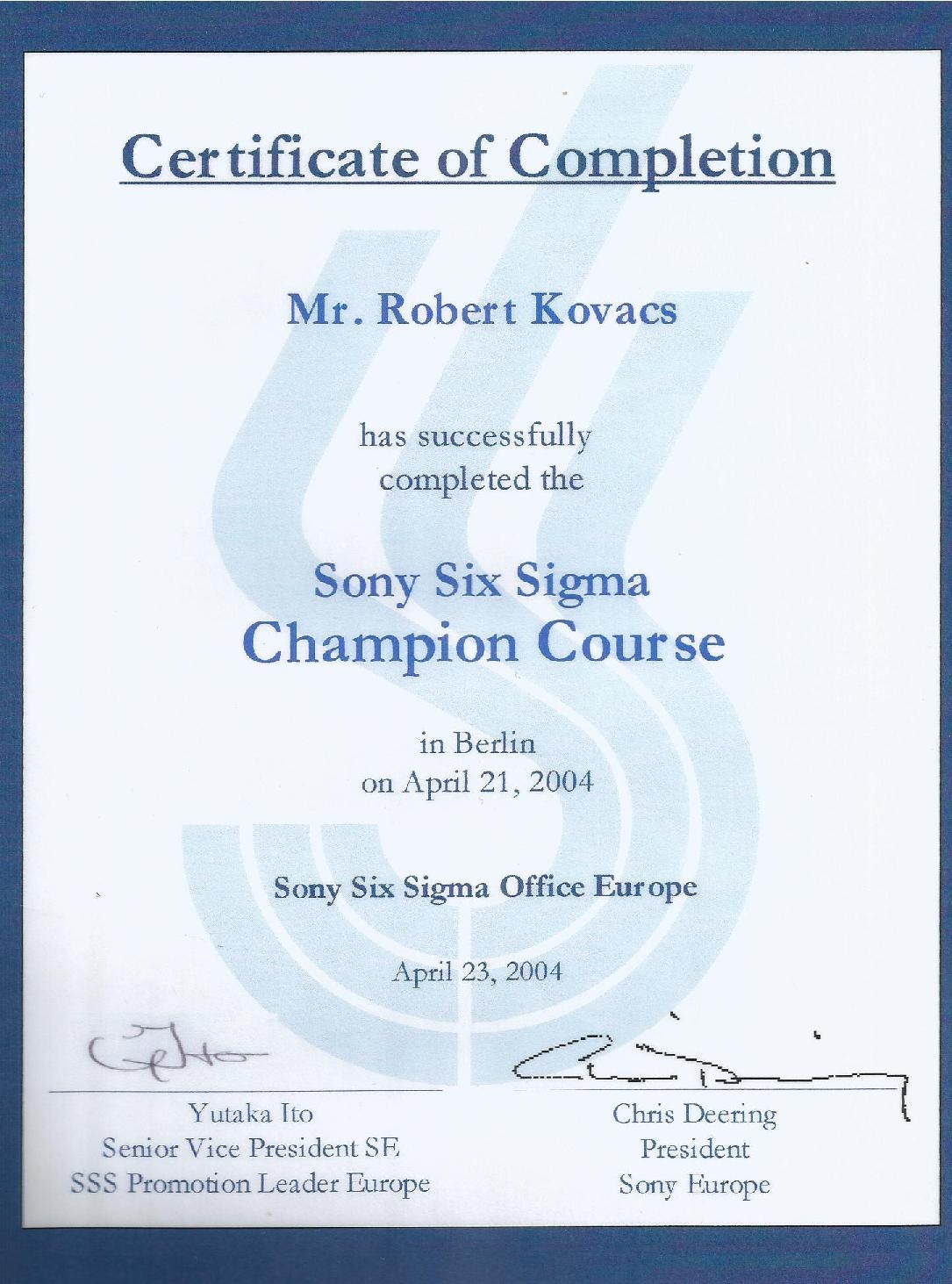

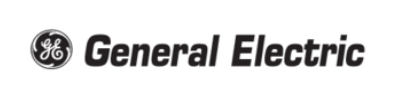
General Electric
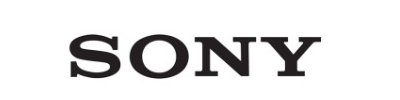
Sony
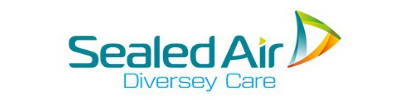